After having his left leg amputated from pediatric osteosarcoma at 6 years old, Colorado State University student Garrison Hayes adapted to wearing a prosthetic limb throughout his childhood.
While the biomedical and mechanical engineering senior adjusted over time, receiving gold and bronze medals at the 2014 USA Paralympic Track & Field National Championships, Hayes’ ambition to assist fellow amputees never wavered. This dream came to fruition after assembling a team for his senior capstone design project.
The team, composed of four other undergraduate engineering students, included Hayes, Thomas Leachman, Eric Gutierrez-Camacho, Lily Lindstrom and Justin Rudrow. Together, they set out to address a gap in the current prosthetic limb market.
“There’s the low-end feet, mid-tier feet and then the high-end feet,” Gutierrez-Camacho said. “(Low-tier) feet can cost $150 to $200, which is very accessible relative to the market, but it can create a wide variety of issues like spine problems or hip deterioration because of that low-quality press setting. And then high-end feet can range from $5,000 all the way up to $50,000.”
The team saw an opportunity to generate prosthetics at a more consumer-friendly price while also enhancing customization levels.
“We kind of saw an opening where we could use 3D printing and be able to make a more comfortable foot for the day-to-day person, for the price of $2,000 to $2,500,” Rudrow said.
Relying on their combined background of biological and mechanical engineering — a five-year program that awards dual degrees in each specification — the team was able to translate evolutionary results into mechanical marvels.
“There’s all these design choices that, like, Mother Nature made that (are) just so intuitive, and it’s really cool to learn about, and then trying to replicate — (that’s) the hard part,” Leachman said.
Together, the team began to conceptualize a foot design they coined The Goldilocks Foot. This design differs from the rigid foot inserts currently on the market, which are created for compatibility with regular shoes.
“All (current foot shells) do is protect the shoe from the insert,” Leachman said. “They offer no support and no sort of active response like a normal foot would. So we’re trying to create a shell that can replace what’s on the market today that’s going to offer better comfort for the user.”
“One of the amputees I interviewed was a woman who said that she would love to have a solution where she could wear (a) high heels prosthetic. And so using that CAD approach that we have for our manufacturing, we can create that contoured S-shape that would fit into a heel.” –Eric Gutierrez-Camacho, CSU biomedical and mechanical engineering student
To further increase comfort for users, the team landed on a Voronoi lattice design for the foot’s structure.
“We went with a lattice structure to hold it all together, and it’s lattice so we can reduce weight as much as possible while also maximizing the amount of support for the energy return,” Leachman said.
The lattice shell is formulated from a carbon fiber and nylon blend that is 3D printed around an internal carbon fiber skeleton insert. The customizability offered by 3D printing originally drew the group to the production medium.
“With the 3D-printing technology that we’re using, we can put it onto any insert,” Hayes said.
To 3D print their initial designs, the team partnered with Corona Prosthetics Inc., a local prosthetics manufacturing company located in Pueblo, Colorado. The partnership granted them access to powder bed fusion printers that can print the entire structure in eight hours.
“So basically it lays down (a) powder form of the filament and then a bonding agent goes on top of it and it sticks it all together, and then it layers it, layer by layer,” Rudrow said.
The team received their first prototype in early January — a moment Gutierrez-Camacho recalled fondly.
“When we received it and we all looked at it for the first time, that was just a huge moment,” Gutierrez-Camacho said. “I felt really proud that we were able to manufacture this.”
Hayes’ unique perspective as an amputee also allowed the group to hear immediate feedback.
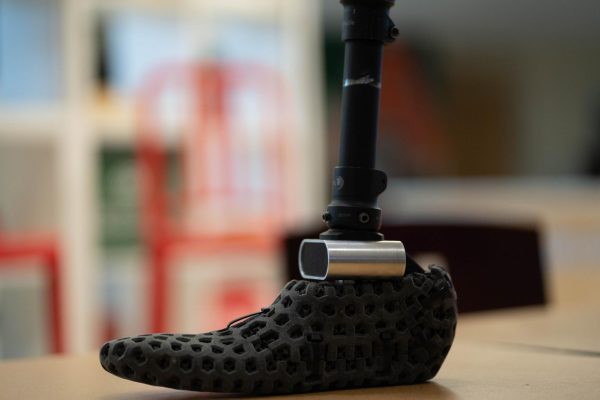
“It was incredibly beneficial, you know, because we’re able to get firsthand advice on what we should change, how it feels, what we could do to address it, and we would just all brainstorm based off of (Hayes’) feedback,” Gutierrez-Camacho said. “So that was incredibly valuable. And him having a technical background as well also helps us to communicate.”
The group also reached out to gather other amputees’ opinions of the project on various Facebook groups. One piece of feedback still stands out to the group because it illustrated the adaptability of the technology.
“One of the amputees I interviewed was a woman who said that she would love to have a solution where she could wear (a) high heels prosthetic,” Gutierrez-Camacho said. “And so using that CAD approach that we have for our manufacturing, we can create that contoured S-shape that would fit into a heel.”
Further testing was performed in the Center for Gait and Movement Analysis at Children’s Hospital Colorado, which hosts floor platforms capable of capturing movement measurements.
“It shows when you step on the force plates, like, how much force you’re applying to the plate and at what direction it’s going,” Lindstrom said. “So you can capture … (a) person walking across and seeing the force distribution. And it’s important to see. There’s certain biomechanics on the natural gait.”
The foot’s longevity was further tested by Leachman at CSU’s Orthopaedic Bioengineering Research Laboratory. The prototype underwent the wear and tear experienced over a normal day’s use.
“We got really nice stress relaxation curves from that, which show that after a certain amount of time with the same stress applied or the same weight, the deformation stays the same,” Lindstrom said. “So it shows that it’s viscoelastic, meaning it returns back to its original shape.”
The team’s accomplishment was recognized March 28 at CSU’s Multicultural Undergraduate Research Art and Leadership Symposium, during which they were declared the winner of the entire event.
“I was a little taken back, for sure, but it was really rewarding,” Lindstrom said. “It was really, like, beautiful to see all the work that we had been doing for a year … kind of be, like, impactful.”
Together, all five students received a provisional patent for The Goldilocks Foot, which they have registered under their newly established startup company Mediflex Prosthetics LLC.
“The fact that we have a patent and all of our names and the company name is pretty cool,” Rudrow said. “I’ve never been a part of anything like that, so it’s really cool to see it, see a product from scratch, until we’re at a point where we can have a patent and that it’s a new design that no one’s thought of before.”
While all five seniors are graduating at the end of the spring semester, they remain committed to the original mission that inspired the creation of The Goldilocks Foot.
“(We’re) just getting more in contact with (amputees) and seeing if we can branch out and get more people to give us their feedback,” Lindstrom said. “That’s what we plan to do, is try and take this and make it a reliable and comfortable product for amputees.”
Reach Katie Fisher at science@collegian.com or on Twitter @CSUCollegian.